3차원 측정
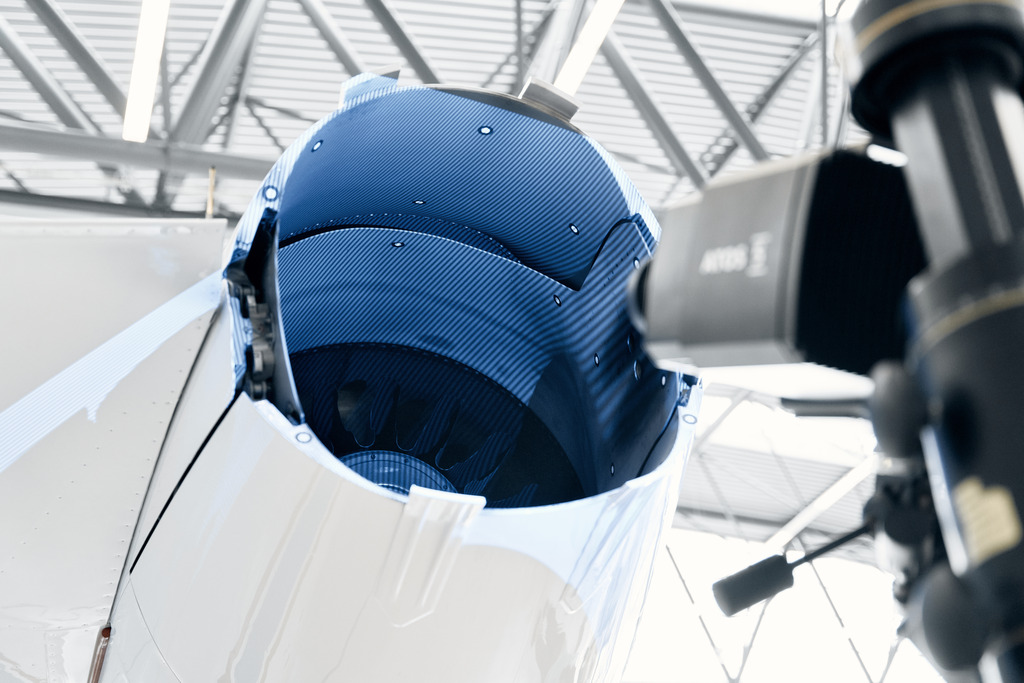
광학식 3차원 측정의 장점
비접촉 측정
이 방법의 가장 큰 장점 중 하나는 비접촉식 측정입니다. 광학식 3차원 측정은 물체에 직접 접촉하지 않고 측정을 수행하므로, 물체의 손상을 방지할 수 있습니다. 이는 특히 미세하거나 민감한 물체에 대한 측정에 있어 매우 유용합니다.
정밀도
또 다른 중요한 장점은 광학식 측정이 가지는 높은 해상도와 정밀도입니다. 이러한 성능 덕분에 복잡하거나 세부적인 형상을 확실하게 측정할 수 있으며, 이는 3차원 형상 분석에 필요한 높은 정밀도를 제공합니다.
유연성
광학식 3차원 측정은 다양한 크기의 물체, 작은 것부터 큰 것까지 모두 측정할 수 있는 유연성을 가지고 있습니다. 또한, 고객의 요구에 따라 고객의 현장에서 직접 측정하거나 고객의 제품을 직접 받아 측정 할 수도 있습니다.
빠른 측정 시간
광학식 3차원 스캐너는 빛을 사용하여 측정을 수행하므로 매우 빠른 속도로 측정할 수 있습니다.
광학식 3차원 측정 과정
스캐닝
구성 요소에 맞게 정확히 세팅 된 면적으로 측정하며 측정 면적의 유연한 선택이 가능합니다.(최대 0.035mm의 정밀도)
포인트 클라우드 생성
짧은 스캔 시간에 높은 포인트 클라우드(개별 측정당 1200만 개의 포인트)를 생성합니다.
다방면 측정 가능
이 방법의 가장 큰 장점 중 하나는 물체를 회전하며 다방면으로 측정이 가능하며, 이는 물체의 다양한 구성요소를 빠르게 3D데이터화 시킬 수 있습니다.
결과
생성된 포인트 데이터를 폴리곤(삼각화된 표면 모델)으로 변환시켜 STL 파일을 생성합니다.
사용되는 장비
ATOS 5
ATOS Triple III
TRITOP
T-Scan Hawk2
품질 검사 | GD&T
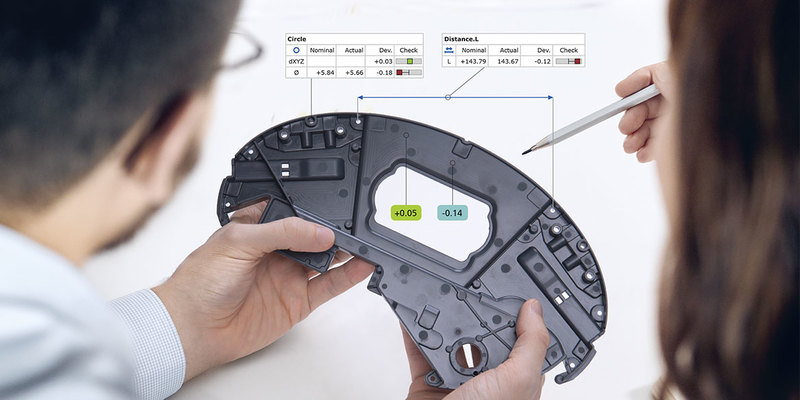
3차원 측정 품질 검사는 제품이나 부품의 공정에서 사용되는 검사 방법 중 하나로, 제품의 3차원적인 특성을 측정하여 품질을 평가하는 것을 의미합니다. 이러한 검사는 제조업 분야에서 매우 중요하며, 제품의 정확성, 정밀성 및 기능성을 보장하기 위해 사용됩니다.
3차원 측정 품질 검사는 주로 다음과 같은 목적으로 사용됩니다 :
- 제품의 치수 및 형상 검사: 제품이나 부품의 치수와 형상을 정확하게 측정하여 제품이 규정된 사양과 허용 범위 내에 있는지를 확인합니다.
- 표면 품질 평가: 제품의 표면 마무리나 표면 상태를 평가하여 표면 결함이나 불량 부분을 식별하고 개선할 수 있도록 돕습니다.
- 조립 및 호환성 검사: 제품이 다른 부품과 정확하게 조립되고 호환되는지를 확인하여 제품의 기능성을 보장합니다.
- 공정 제어 및 문제 해결: 생산 공정 중에 제품의 품질을 지속적으로 모니터링하고 문제가 발생할 경우 신속하게 대응하여 생산성을 향상시킵니다.
3차원 측정 품질 검사는 다양한 방법과 장비를 사용하여 수행됩니다. 이러한 방법에는 측정기기를 사용한 접촉식 또는 비접촉식 측정, 광학 측정, 레이저 스캐닝 등이 포함됩니다. 이러한 기술들은 정밀한 측정과 빠른 결과 획득을 가능하게 하여 제품의 품질을 효과적으로 평가하는 데 도움을 줍니다.
역설계
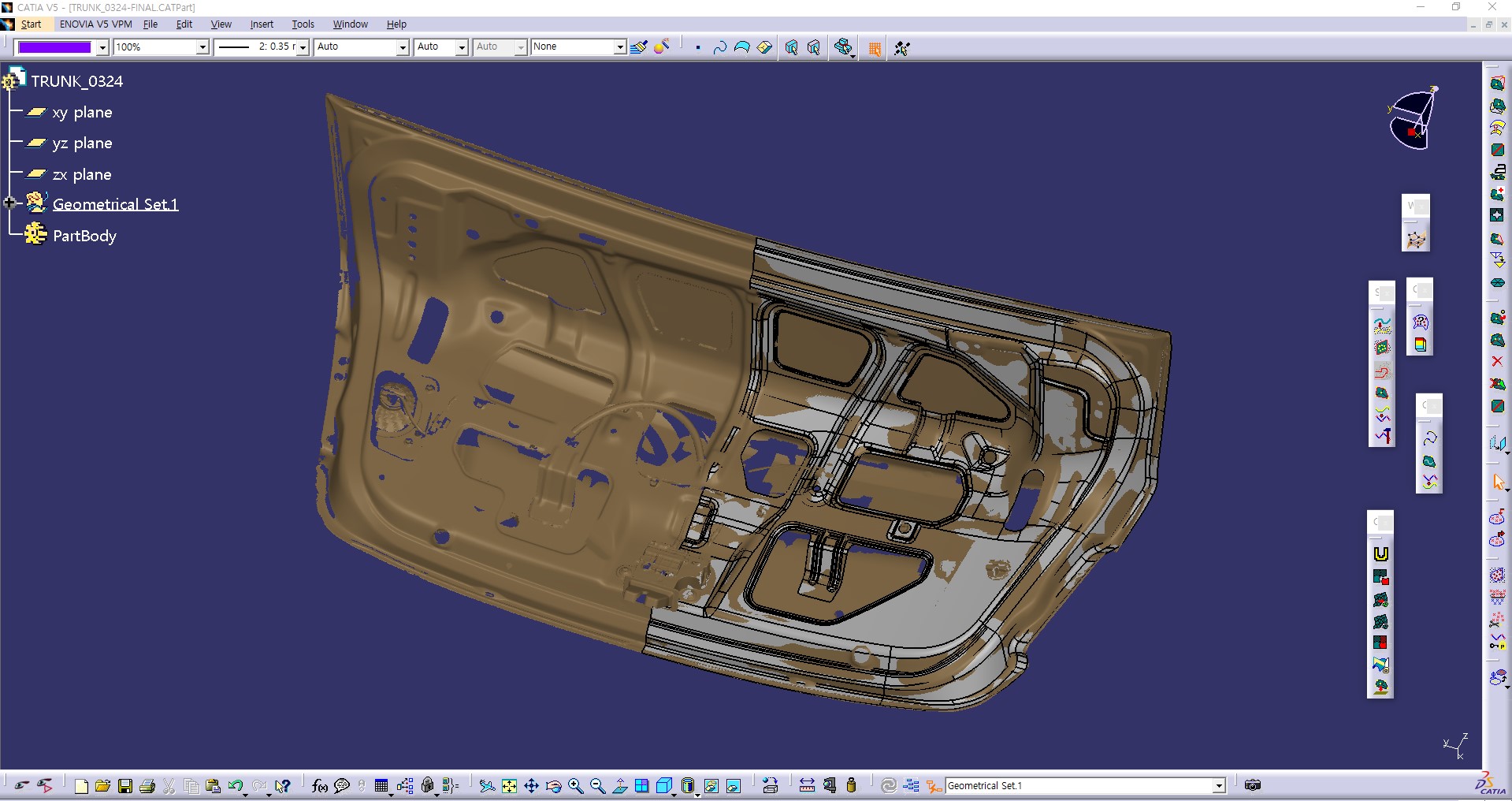
역설계는 다양한 산업 분야에서 활용됩니다. 예를 들어, 제조업에서는 고전적인 제품이나 부품의 디지털화를 통해 효율적인 생산 과정을 구축하거나 기존 제품의 개선을 위해 사용될 수 있습니다.
이러한 3차원 역설계 과정은 주로 CAD(Computer-Aided Design) 소프트웨어나 3D 스캐닝 기술을 활용하여 수행됩니다. 이를 통해 디지털화된 3차원 모델은 후속 작업에 활용되어 제품 혹은 구조물의 설계, 분석, 시뮬레이션, 제조 등 다양한 과정에 활용될 수 있습니다.
역설계 사례
https://youtube.com역설계는 주로 제품이나 구조물의 실제 모양이나 형태를 디지털 3차원 모델로 재구성하는 과정을 말합니다. 이는 기존 제품이나 구조물의 실제 모습을 파악하여 디지털 모델로 변환하고, 이 모델을 활용하여 다양한 분석, 수정 또는 재설계 작업을 수행하는 데 사용됩니다.
역설계는 다양한 산업 분야에서 활용됩니다. 예를 들어, 제조업에서는 고전적인 제품이나 부품의 디지털화를 통해 효율적인 생산 과정을 구축하거나 기존 제품의 개선을 위해 사용될 수 있습니다.
이러한 3차원 역설계 과정은 주로 CAD(Computer-Aided Design) 소프트웨어나 3D 스캐닝 기술을 활용하여 수행됩니다. 이를 통해 디지털화된 3차원 모델은 후속 작업에 활용되어 제품 혹은 구조물의 설계, 분석, 시뮬레이션, 제조 등 다양한 과정에 활용될 수 있습니다.